SINGLE LAYER |
PRODUCT PERFORMANCE |
DIELECTRIC PERFORMANCE |
OTHER |
Part Number |
Thickness1[.000"/μm] |
Thermal Performance2[°C/W] |
Impedance3[°C in2/W] / [°C cm2/W] |
Conductivity2[W/m-K] |
Breakdown5[kVAC] |
Permittivity6[Dielectric Constant] |
Dielectric Conductivity4[W/m-K] |
Glass Transition7[°C] |
Peel Strength8[lbs/in] / [N/mm] |
HPL-03015 |
1.5/38 |
0.30 |
0.02 / 0.13 |
7.5 |
5.0 |
6 |
3.0 |
185 |
5 / 0.9 |
HT-04503 |
3/76 |
0.45 |
0.05 / 0.32 |
4.1 |
8.5 |
7 |
2.2 |
150 |
6 / 1.1 |
HT-07006 |
6/152 |
0.70 |
0.11 / 0.71 |
4.1 |
11.0 |
7 |
2.2 |
150 |
6 / 1.1 |
MP-06503 |
3/76 |
0.65 |
0.09 / 0.58 |
2.4 |
8.5 |
6 |
1.3 |
90 |
9 / 1.6 |
HR T30.20 |
3/76 |
0.9 |
0.15 / 0.97 |
1.5 |
7.5 |
7 |
1.0 |
90 |
9 / 1.6 |
测试方法Method Description:
1 – Optical 5 - ASTM D149
2 - MET-5.4-01-40000-Test Thermal Perforamnce of IMS 6 - ASTM D150
3 – Calculation from ASTM 5470 7 –MET-5.4-01-7800
4 – Extended ASTM 5470 8 –ASTM D2861
Note: For applications with an expected operation voltage of 480 Volts AC or above, Bergquist recommends a dielectric thickness greater than 0.003" (76μm).
Note: Circuit design is the most important consideration for determining safety agency compliance.
Breakdown Voltage does not represent max operating or proof test voltage.
■ Thermal Clad Long Term Reliability
New materials undergo a rigorous 12 to 18 month qualification program prior to being released to the market.
In state-of-the-art laboratories and test facilities, Bergquist performs extensive testing on all their thermal materials for electrical integrity. Bergquist utilizes stringent development procedures outlined in Bergquist document #Q-6019. The lab facilities at Bergquist are UL certified and manufacturing facilities are ISO 9001:2000 certified.
Extensive qualification testing consists of mechanical property validation, adhesion, temperature cycling, thermal and electrical stress. To validate long term reliability, electrical testing is performedat selected intervals to 2000 hours where final evaluation is completed.
To ensure consistent product performance with materials manufactured, we couple the up-front qualification test with ongoing monthly audits. These audits include physical, electrical and thermal property tests.
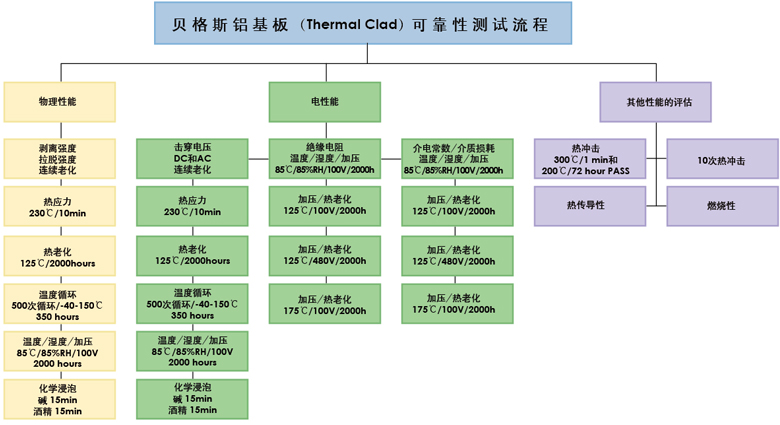
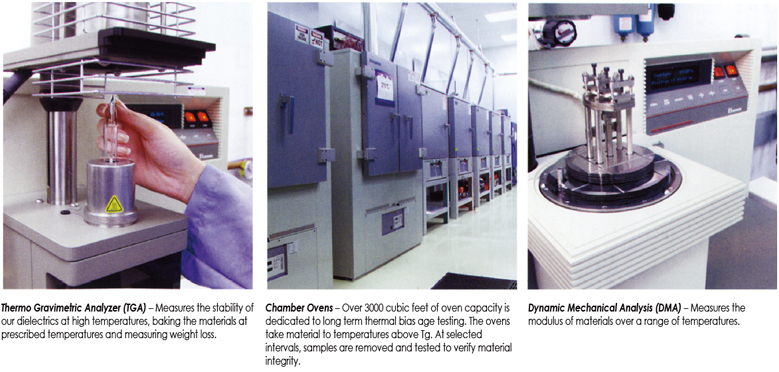
■ Dielectric Performance
The technology of Thermal Clad resides in the dielectric layer. It is the key element for optimizing performance in your application. The dielectric is a proprietary polymer/ceramic blend that gives
Thermal Clad its excellent electrical isolation properties and low thermal impedance.
The polymer is chosen for its electrical isolation properties, ability to resist thermal aging and high bond strengths. The ceramic filler enhances thermal conductivity and maintains high dielectric
strength. The result is a layer of isolation which can maintain these properties even at 0.003" (75μm) thickness. This guide will help you select the best dielectric to suit your needs for watt density, electrical
isolation and operating temperature environment.
Dielectrics are available in thicknesses from 0.003" (75μm) to 0.006" (150μm), depending on your isolation needs.
Thermal impedance is the only measurement that matters in determining the watt density capability of your application because it measures the temperature drop across the stack-up for each watt of heat flow. Lower thermal impedance results in lower junction temperatures. The lower the thermal impedance, the more efficiently heat travels out of the components.
High thermal conductivity is relevant to your application when the thickness of the dielectric material is taken into consideration. Impedance to heat flow is proportional to the ratio of thickness to thermal conductivity.
■ Bergquist TO-220 Thermal Impedance Testing of IMS
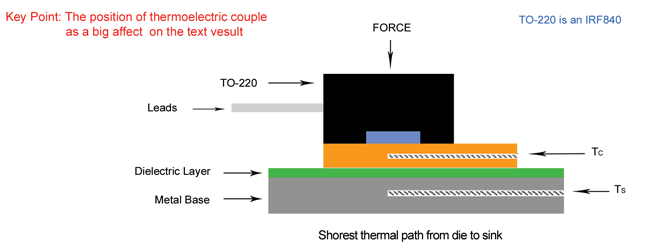
■ Solder Assembly
Solder joints deserve additional consideration in the design of Thermal Clad assemblies. This section covers solder surface finishes, application and thickness, alloy and flux.
Standard circuit board finishes are available for Thermal Clad circuit boards. These finishes are RoHS compliant – ENIG (Electroless Nickel/Immersion Gold), OSP (Organic Solderability Protectant), immersion silver or tin and lead-free HASL. The standard tin/lead HASL is also available. Shelf life of Thermal Clad circuit board finishes varies from 3 to 6 months for OSP and up to 1 year for ENIG or HASL. The plated finishes and OSP provide a thin planar coating to protect copper base layers from oxidation. The ENIG finish supports aluminum wire bonding. A thicker gold is required for gold wire, so electroless gold or palladium finish can be added to the ENIG process.
Note: For copper-based Thermal Clad, the soldering process should not exceed 260°C for one minute and for aluminum base Thermal Clad should not exceed 300°C for one minute. See graph below which references a typical oven reflow temperature profile.
|